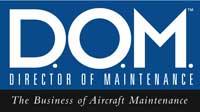
The Zero Factor Fallacy
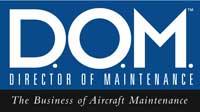
Have you ever wondered why we don’t follow the procedures, why we are having the same safety incidences, why we are always incurring those same mistakes? The scientific evidence is counter intuitive to typical management quality and safety activities. One thing has been patently clear: the command and control micro-management style is not working. This style is characterized by creating a new procedure for every new problem, handing down administrative punishment for those who commit infractions and demanding that the workforce to be compliant. It is a knee-jerk reaction to which we have become accustomed.
Here is where you are going to start to scratch your head. Messages like “zero accidents” or “zero defects” or “zero tolerance” from upper management send a mixed message because they are just words without substance. They actually exacerbate what they purport to denounce. The pursuit of “zero” sets an unachievable goal — an admirable one, but nonetheless unachievable because you seek perfection. In Management 101, you learn that setting unachievable goals frustrates the workforce and reduces productivity. With a “zero mentality,” anything less than zero is a failure. Why put forth extra effort or any effort since failure is inevitable? You alter reality when other methods are devised to achieve the perception of “zero” to pacify management.
The argument will come up that if I am not pro “zero accidents”, “zero defects” and “zero tolerance,” then my goal is to plan for accidents and defects to occur and I’m tolerant of all aberrant behavior. This is thought-limiting mentality and binary thinking. The fact that I see the fallacy in perfection doesn’t mean that I pursue imperfection. On the contrary — I recognize imperfection for what it is. I also recognize that the phrase “all incidents are preventable” is hindsight thinking that cannot predict future events, as many may think. Don’t get me wrong — we need that hindsight as a learning tool to keep from committing the same error, but it is not going to be predictive. We don’t know what the future has in store for us and we can only surmise what might occur and prepare.
The pursuit of perfection
Let’s look at the zero fallacy. Would you have graduated any class in school if the passing score was 100 percent and anything else was a failure? Few, if any of us, would graduate. What do you think that kind of policy would spawn? Do you think it would create more tension and stress in the classroom, increased cheating, possibly theft of tests and bribery? This drives everything underground. What about the level of learning in that environment? The focus would be more on how to obtain the 100 percent and keeping the unethical methodology cloistered than in learning anything. The same holds true with the pursuit of perfection. It promotes behavior that it espouses to reduce.
Don’t think this can happen? During a conference with Secretary of the Air Force, it was stated that the impetus of cheating was, “… spotty morale, micromanagement and an unhealthy training environment with insistence that everyone get 100 percent on exams when 90 percent was the standard.” This instilled an atmosphere of fear amongst the missile crews that pushes past stress (which can be beneficial) into distress, which is counter productive.
Let’s get down from the pulpit in preaching zero accidents and zero defects and talk reality. Zero tolerance is a slightly different animal that I will discuss shortly.
I first came to observe this phenomenon of compliance and command and control while working for an airline many years ago. The maintenance was run by the lead mechanics. Supervisors were relegated to administrative duties in support of the mechanics. The oversight we had was ourselves — as a close knit group, we watched out for each other because one person’s action reflected us all. We started to rent half of our hangar to another airline that had heavy supervision and tight controls over all activities. What amazed me is that with all the oversight, controls and resources the other airline had, they also suffered from a high accident rate and quality escapes. After many years had passed, I wound up working for that other airline. Some of the mechanics commented on those times when we shared the hangar, that they were amazed that we had so few accidents and quality escapes with fewer resources available and no oversight. I hadn’t discovered the reason until I started to study human behavior.
You would think that the organization with the higher level of oversight and tighter controls would have the lowest amount of accidents and quality escapes, but the opposite is true. The reason is the emphasis on compliance. Don’t get hurt, work safe, do it right the first time, etc. That all sounds like a good thing, right? It is, up to a point, but if compliance is all you have, you have a labor-intensive and ineffective operation.
The role of compliance
People will be compliant only when they are being watched. Don’t believe me? If you travel a road every day and the speed limit is 30 mph, what is the speed most people are going? Maybe 35 mph or more? We have become accustomed to a safety buffer of 5 mph over the limit but that is not compliant, is it? What speed does everyone go when there is a cop car on the side of the road? Everyone is doing 30 mph on the nose.
You need oversight everywhere in order to ensure that the workforce is compliant. We have supervisors, but who watches the supervisors to ensure their compliance? Managers, but then who watches the managers? And so on until you have created this hierarchy of police. Is the solution to remove all oversight? Just because one premise is not true doesn’t mean the opposite is true. You’re back to binary thinking. If all you see are nails then every solution is going to involve a hammer.
What you want to do is create an environment of learning. We learn from others transferring what they have learned, typically through their mistakes or mistakes of their predecessors. The most profound learning experience is from our own mistakes. If mistakes are not tolerated, learning will not take place and compliance is the only avenue you have allowed in your organization. This is where “all incidents are preventable” comes in as a learning tool to prevent repeat occurrence only; it does not predict future events. In order to learn, you also need the latitude to expand.
Zero means zero
Maintaining the goal of perfection does not allow any deviation. Zero accidents means you have to take into account everything including paper cuts. Zero defects means the grains of salt on your steak must be evenly distributed at 2 mm apart — no deviation is allowed in perfection. You might say well that’s ridiculous, and you’re right, but zero is zero. It is finite, an absolute, no deviation is allowed. Ask this in your “Zero” environment: is management held at the same zero defects criteria? If you espouse zero but really don’t mean zero, then what is your definition of zero? Is your message that you really don’t mean what you say? I’m confused and everyone else will be, too.
If you want to look at this mathematically, zero adds nothing and takes nothing away — but if you multiply by zero, whatever was disappears. We can’t have math without zero but it lacks substance by itself and it can be very confusing. All you have to do is look back at our dilemma in declaring the new millennium in the year 2000. The new millennium actually started in 2001. If I asked you to give me a 10 count, do you start with zero or one? Most people will start with one and end with 10. For harmony’s sake, we typically see the year 2000 as the beginning of the new millennium and avoid the conflict. So much for “zero tolerance”.
“Zero tolerance” is upper management’s policy of giving ultimate authority to subordinates while removing all thought processes. Upper management believes that those so ordained are incapable of rational thought, therefore they have eliminated all capacity to think. You are an automaton and your duty is to act without thought. Do as you’re told and don’t ask questions.
“Zero tolerance” for drug abuse in the schools would expel students for sniffing markers. Markers are scented for them to smell but zero is zero, no deviation allowed. “Zero tolerance” for speeding would get you a ticket for doing 31 mph in a 30 mph zone. This has to assume that the radar is perfect, your speedometer is perfect, the officer’s vision is perfect, the road condition is perfect ... need I continue?
Perfection and imperfection
In a perfect world, it would be easy to find imperfections — but then again, in a perfect world there would be no imperfections. Just think of all the people this would put out of work: police, fire department, repair personnel, judges, jailers, anyone involved in maintenance, etc. You would not need a thermometer because the temperature would be perfect constantly, weather forecasters would be out of work although the polar ice caps might complain but the higher water levels would not materialize because everything is perfect.
What is perfect for one person is not perfect for another, so we have to be uniformly perfect as well — looking identical, thinking identically and acting identically. Fortunately, I don’t live in that world of clinical monotony. I am rational enough that I don’t expect perfection and I’m irrational like the rest of humanity. I enjoy imperfections because they make life interesting.
Perfection versus imperfection is one binary train of thought I will accept, and only because they are not polar opposites. It’s not perfect versus imperfect, but rather imperfection that is comprised of many shades of grey. Intolerance for some aberrant behavior is required and action should be taken, but the action must be commensurate with the aberrant behavior. Which would be a rational response: removing the scented markers and replacing them with unscented markers, or leaving the unscented markers and expelling students for sniffing them? Issuing a warning that you were 1 mph over the speed limit or a $100 traffic ticket? You removed the temptation in one instance. Deviant actions are typically system based rather than behavior based. Therefore, fix the system, not the person. However, don’t we seek a victim as managers? It’s a clean cut solution but doesn’t fix the problem. In the other, the $100 ticket fuels contempt for the system, fosters aberrant behavior and the only lesson learned is to be compliant only when you have to be, and that people will speed as often as they can without being caught.
What do you think?
If compliance isn’t the way to go, what is? When the two airlines I mentioned shared the hangar, the one with the least oversight and controls had the least accidents and quality escapes. The reason is that the airline mechanics evolved from indifference, compliance and watching out for one’s self to engaged, mutual respectful and cooperative behavior. They did not have superiors ensuring their compliance but co-workers looking after other co-workers to ensure the norm of cooperation. This is not the same as adhering to the norm of the status quo, as that is back into lock stepping to the same tune. In adhering to the norm of cooperation, you are working in unison with the freedom to question the direction. Everyone is thinking.
When everyone is thinking, the problem arises when everyone is thinking alike. This is group think and it inhibits innovation. It is also a problem when everyone thinks differently and no one progresses, as everyone has their own agenda either because of blind ambition or self-protection. In any case, this train of thought is spawned by the prevailing management system.
If you are wondering why you have so many accidents and quality escapes, try this quick test for your organization. Are you always seeking what is wrong instead of what is right? Are there more punishments being dealt out than praise? Your answers to these two questions will show where your focus lies. If it is heavy on the negative, you are in a fire fighting stage and trying to put out the flames with gasoline. You should be more proactive in your measures, but telling someone that fire extinguishers are handy doesn’t help someone who’s watching his or her house burning down.
Now for a discouraging word: you will never get out of the fire-fighting stage. It will always exist. Mistakes will be made. A mistake is not a problem but repeating them is. The mission is to fight lesser fires as time goes on and do more proactive fire preventive measures. “If it’s broke, fix it. If it’s not broke, improve it.” To be proactive requires open communication with the freedom to challenge the status quo without retaliation. Everything is above board — accept imperfection as reality and see it as an opportunity to learn and grow.
An eight-cylinder engine is more efficient than eight one-cylinder engines.
Patrick Kinane is an FAA-certificated A&P with IA and commercial pilot with instrument rating. He has 50 years of experience in aviation maintenance. He is an ASQ senior member with quality auditor and quality systems/organizational excellence manager certifications. He is an RABQSA-certified AS9100 and AS9110 aerospace industry experienced auditor and ISO9001 business improvement/quality management systems auditor. He earned a bachelor of science degree in aviation maintenance management, a master’s of science degree in education, and a Ph.D. in organizational psychology. Kinane is presently a senior quality management systems auditor for AAR CORP and a professor of organizational behavior at DeVry University.