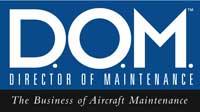
Maintaining Compliance vs. Managing Compliance - There’s a Big Difference
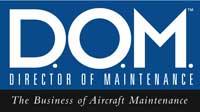
By Joe Hertzler
In our professions, we are continuously surrounded by maintenance records like manual revisions, bulletins and alerts, discrepancies and the paperwork required to return an aircraft to service. The paper trail never ends. While safety the overall reason for all this paperwork, compliance is our goal.
Compliance with the regulations, OEMs and your own operational specifications greatly enhances the safety of your operation — but is safety the sole reason to maintain compliance? While safety should be reason enough to maintain compliance, it is important to understand that compliance, when managed efficiently, can have a profound effect on other important business aspects.
In order to understand the effects of maintaining compliance versus managing compliance better, let’s first look at the typical maintenance cycle.
The Maintenance Cycle
The maintenance cycle for an aircraft is made up of four basic segments.
Segment 1 - Aircraft In Service
The first segment represents the time in which the aircraft is flight ready or in flight. Once the aircraft is delivered (either new from the factory or fresh out of maintenance) to the owner for use (approved for service or return to service) the aircraft-in-service segment of the maintenance cycle begins. The length of this segment is limited due to two factors: scheduled maintenance and/or component failure. It is important to note that the scheduled inspection program for an aircraft is purposefully designed to eliminate component failure, though it does happen and must be considered. As the aircraft is operating in the aircraft-in-service segment, it is accumulating hours, cycles and calendar time.
Segment 2 - Inspection
The next segment of the maintenance cycle is the inspection segment. Recurring inspections performed on a scheduled basis are supposed to identify unsafe conditions that, when corrected, ensure safe operation for that period of time in between scheduled inspections. The inspection segment is the physical action that qualified individuals take to find defects that have developed as a result of the aircraft-in-service segment. An aircraft inspection requires the use of a checklist. The obvious purpose of the checklist is to avoid forgetting any portion of the inspection and to allow an inspection program to be divided up into a logical and adequate schedule.
The other common part of the inspection segment is the logbook evaluation or audit. The purpose of the audit is to determine the current status of the aircraft and identify any deficiencies in the aircraft’s maintenance records. During the inspection phase, all discrepancies found are recorded and it must then be determined what discrepancies need corrected.
Segment 3 - Corrective Action
The corrective action segment is when maintenance is performed in accordance with appropriate instructions to correct the physical defects and records deficiencies identified. It is the proper correction of the discrepancies found that determines the airworthiness of the aircraft. If all “airworthiness” issues have been corrected, the aircraft is then approved for return to service. When defects and deficiencies that impact the airworthiness of the aircraft are left undone, the inspection performed is still signed off. However, “a list of uncorrected discrepancies” must be provided to the owner/operator and the aircraft should not be operated until those items are corrected.
Segment 4 - Modification
The fourth and final segment in our definition of a maintenance cycle is the modification segment. Often, an aircraft owner will decide that the aircraft would better fit their needs if it were modified. Modifications are either major or minor in nature. The reason to include the modification segment in the maintenance cycle is the possible impact modification can have on the inspection segment. According to regulatory policy, all major modifications should come with instructions for continued airworthiness (ICAs). These instructions may include new inspection and/or maintenance requirements that must be meshed into the current inspection program for the aircraft. The two basic regulatory methods of approving modifications are supplemental type certificates and field approvals, the latter of which steadily less common.
After we return the aircraft to service, we start the cycle all over again. We begin with the aircraft-in-service segment and continue the maintenance cycle for the life of the aircraft.
Maintaining Compliance vs.Managing Compliance
The difference between maintaining compliance and managing compliance efficiently comes down to knowledge and planning. By having complete and accurate maintenance records, you can make the maintenance cycle more predictable and less expensive. Read on for the effects of having accurate and complete maintenance records and by using that information to better plan for maintenance.
Minimize Downtime
One of the most costly expenses that an aircraft owner/operator incurs (though somewhat intangible), is downtime. Because the aircraft is an asset to the company, it usually has an ongoing interest cost (regardless of its availability for use). Add to that the cost of alternative transportation and the possibility of lost business from the company’s inability to act quickly (one of the reasons they bought the aircraft in the first place), and you can see how unnecessary and unplanned downtime must be avoided. The only way to manage downtime is to get your arms around the maintenance requirements and the utilization of the aircraft and plan the maintenance to be accomplished effectively. Try to accomplish everything that will come due before the next scheduled inspection whenever possible and plan to modify the aircraft in conjunction with an inspection.
Reduce or Eliminate the Duplication of Work
Duplication of work is likely the second-largest unnecessary expense for aircraft owners and operators. If the scheduled inspection or maintenance accomplished is not properly recorded in the maintenance records of the aircraft, time is either wasted chasing down a revised maintenance record or, in the worst case scenario, the maintenance will be duplicated. As they say, “no job is finished until the paperwork is finished.” The rules clearly require that the operator examine the maintenance records prior to returning the aircraft to service. This not only ensures the aircraft has been approved for return to service, but just as importantly, ensures all required maintenance entries have been made. The paperwork is never as much fun as fixing the aircraft.
As maintenance providers, we should encourage the operator to look over the entries as a second set of eyes. Additionally, the operator should understand the importance of making sure entries are complete and accurate and take the time look them over. Most maintenance providers would much rather make needed corrections up front than get a call in six months to ask for a new entry. We are all susceptible to making mistakes. As logbook auditors, we commonly find omissions, inaccurate times/cycles, wrong dates, etc.
When It’s Time to Sell
Not only do accurate and complete maintenance records have a significant impact on the ongoing operational cost of an aircraft, the overall value of the aircraft is impacted as well.
Arguably, the most revealing pre-buy inspection is a good audit of the aircraft records. A complete audit will identify the current status of the aircraft as required by 14 CFR 91.417, uncover time frames of no maintenance, and identify inaccurate engine cycle tracking, as well as aircraft time tracking and reveal aircraft damage history. Once an aircraft has been damaged, it is difficult to establish a value that is as high as the identical aircraft with no damage — for our purposes, we will assume that the damage was unavoidable. (Accidents just happen.) However, we can control the records. So, it is important to realize that incomplete or missing records will greatly impact the value and ability to sell the aircraft.
At Avtrak, we have seen missing blocks of time or missing logbooks impact the value of a used aircraft as much a 25 percent. For a $2.5 million aircraft, that equals $625,000! Hard to believe? Think about this: if your particular aircraft is one of several (10 or 20) available when you are ready to sell it and you are missing a large block of maintenance records for some reason, the aircraft with complete and accurate records will sell first. When you are faced with a must-sell situation, you will be forced to reduce the price significantly in order to move the aircraft. Complete and accurate aircraft records are cheap insurance when compared to the long-term effects of letting them go.
In the end, we all strive to maintain compliance — but there’s a big difference between maintaining compliance and managing compliance. The difference comes down to having accurate, well-organized records and planning well in advance for upcoming maintenance.
Joe Hertzler is CEO and co-founder of Avtrak. He has more than 25 years of experience in the industry and is well known for his in-depth understanding of maintenance regulations and how they affect aircraft compliance. He often speaks on the topic of maintenance compliance at industry events, such as the NBAA Maintenance Managers Conference, PAMA meetings and IA renewal seminars. He also serves on the National Air Transportation Association’s (NATA) Maintenance and Systems Technology committee. For more information, visit www.avtrak.com.