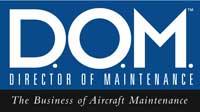
Approval for Return to Service - No Job is Finished Until the Paperwork is Done!
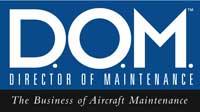
I recently found myself in a surprisingly serious conversation regarding the term “return to service” and what date should be used as the “official” return-to-service date. The question came up as a result of the use of task cards created from within a commercial maintenance tracking system to complete work where the total work scope spans several weeks or months and includes many date-sensitive scheduled maintenance items. The discussion struck me as such a surprise that I felt obliged to research the topic and get the truth out and in front of all of us. As it turns out, it can be complicated and taking the wrong position will only penalize the operator. I have a passion for maximizing aircraft availability, so I ask you to carefully consider the facts and details within this article in the course of aircraft maintenance and the recording thereof.
The question at hand for this article is: what is the official return-to-service date? Is it 1) The date on each individual task card signed off by the individual technician(s) in the course of performing the work or, 2) the date of the maintenance logbook entry created by the maintenance organization upon completion of the work?
To begin with, we need to come at this from a 100,000-foot view. Let’s start by reviewing some of the pertinent regulations that affect return to service and time in service.
Firstly, here’s the definition of “time in service” from FAR Part 1: “Time in service, with respect to maintenance time records, means the time from the moment an aircraft leaves the surface of the earth until it touches it at the next point of landing.”
It seems pretty self-explanatory, but pertinent for this discussion, time in service is defined as the time elapsed from the time the aircraft leaves the ground to the time it touches back down. From the standpoint of the hours accumulated and the landings accumulated on an aircraft, the aircraft accumulates time only when it is operating in the air.
Next, let’s refresh our memory about the term “return to service.” Like most terms in the regulations, the term return to service is not specifically defined. However, we do know this: in FAR Part 43, which relates to maintenance, preventive maintenance, rebuilding and alteration (specifically both 43.9 and 43.11), the rule uses the phrase “approved for return to service.”
FAR Part 43.9 (a) (4)
(4) ... person approving the work. The signature constitutes the approval for return to service only for the work performed.
FAR Part 43.11 (a) (3)
(3) … certificate held by the person approving or disapproving for return to service the aircraft ...
Additionally, FAR Part 91 tells the operator of the aircraft that they cannot return the aircraft to service until the maintenance records are complete and the aircraft is approved for return to service.
FAR Part 91.407 (a) (1)
(a) No person may operate any aircraft that has undergone maintenance, preventive maintenance, rebuilding, or alteration unless ...
(1) It has been approved for return to service by a person authorized ...
The use of this language clearly draws a distinction between the approval for return to service and the actual act of returning the aircraft to service. Better said, approval for return to service is a maintenance function and returning the aircraft to service is the act of causing the aircraft to lift off the ground. The definition of time in service discussed earlier brings clarity here.
Next it is important to define maintenance. Fortunately the FAA has done so. FAR Part 1 states “Maintenance means inspection, overhaul, repair, preservation and the replacement of parts, but excludes preventive maintenance.”
Specifically note that maintenance does, in fact, include inspection.
I have also found a great place to look for information that helps to clarify regulations and the intent of those regulations is within the FAA’s own guidance and policy documentation. I encourage you to make a note of this web site if you don’t already know about it. (Visit http://fsims.faa.govFlightStandardsInformationManagementSystem. This is the Web site that contains much of the guidance material used by FAA safety inspectors while doing their jobs. Although the information contained within the guidance material is not regulatory, it does provide clarification in many cases of the intent and the interpretation of the regulations.)
For the purpose of this article, there is a clause within that FAA guidance material that provides clarification for us with respect to the question at hand. That clarification is located in (get ready, this is a mouthful) FAA Order 8900.1, Change 36, Volume 6 Surveillance, Chapter 1 Part 91 Inspections, Section 2 “Monitor Part 91 and Approve/Monitor a Part 91 Subpart K Program Manager’s Aircraft Inspection Program,” Paragraph 6-42 Inspection Programs, A, 2),f) which states: “The inspection is not considered complete until the required recording procedures of §§ 43.11 and 91.417 are met.”
Now, let’s look again at the question at hand. What is the official return-to-service date? Is it 1) the date on each individual task card signed off by the individual technician(s) in the course of performing the work or, 2) the date of the maintenance logbook entry created by the maintenance organization upon completion of the work?
Task cards
What is a task card, anyway? An individual task card is a product created by a commercial maintenance tracking system. In addition to the actual maintenance instructions from the aircraft manufacturer required to complete the work, a task card also provides a place to capture all of the information needed to approve an aircraft for return to service for that specific maintenance task, like part numbers and serial numbers removed and/or installed, measurements taken as a result of an inspection, torque values used, resulting discrepancies or defects, etc. A task card is most useful if it allows you to capture all of the information required by FAR Part 91.417 “Maintenance Records,” FAR Part 43.9 “Content, form and disposition of maintenance ...,” and FAR Part 43.11 “Content, form and disposition of records for inspections ...”
The task card is an instrument created in conjunction with the maintenance tracking system and is very handy for quickly meeting the maintenance record keeping requirements of Part 43.9 and Part 91. However, the task card rarely becomes the official aircraft maintenance record simply because it doesn’t easily fit into the conventional logbook form of aircraft maintenance record. Some of us do indeed use the task card as an official permanent maintenance record when single tasks are accomplished quickly during a short maintenance event, but because maintenance records can have such a large impact on the value of the aircraft, maintenance logbook entries are usually created and entered into the permanent aircraft logbooks.
The task card takes on another specific role when the aircraft is going to be in maintenance for any length of time and there are several tasks to be accomplished. In that case, the task cards are more useful for work instructions, the organization of the work to be accomplished, and to capture the pertinent details associated with the task as it is being accomplished. For large planned maintenance events, the work scope will consist of a long list of items that need to be accomplished and the aircraft will be down for maintenance for a while as the work is being done. In the end, the maintenance event will all be summarized in an aircraft maintenance logbook entry and become a part of the permanent aircraft maintenance record.
Resulting documentation
For the sake of conversation and clarity, let’s look at what documentation we have in front of us at the end of such a maintenance event. We have a large stack of task cards, all of which include the same hours and cycles/landings but several different dates indicating specifically when the work was accomplished as a part of the work scope. In addition, we have a logbook maintenance entry that contains a detailed summary of each maintenance item referred to on the task cards, and that also includes the hours and cycles/landings as well as the date of approval for return to service. Now, let’s focus on just one specific maintenance item in the long list of items. For example’s sake, let’s say it’s some landing gear inspection that is required every 12 months. As a part of the maintenance event, the landing gear inspection was accomplished on the Jan. 15 as indicated by the task card completion. The maintenance logbook entry is dated March 15 and is signed and meets all of the requirements of Part 43.11. In the purest sense, the maintenance records indicate that the work was accomplished twice. The task card says the inspection was accomplished on Jan. 15 and the logbook entry indicates it was accomplished on March 15. We all know it wasn’t accomplished twice, and this is where the confusion comes in.
Some would argue that the date that must be used to calculate the next due is March 15 because that is the date on the task card. This is simply not true. I ask you this: when the work being accomplished is documented in a work order system of a repair station, or even just as a part of a less organized process by an independent maintenance technician, does the actual accomplishment date of the item count for the next due calculation or the date of the final logbook entry that summarizes the work accomplished? The answer is simple. It is always the date of the logbook entry — or better said, the date of approval for return to service.
Exceptions
There are a few exceptions to this truth —they will become clear as I explain them. For the purposes of maintenance tracking, I refer to these unique maintenance task exceptions as “special date items.” Special date items are those items that are due based upon something other than the date of approval for return to service. Some examples include oxygen bottles that have been hydrostatically tested, fire bottle squibs that are due to be replaced based upon a shelf life or useful life (whichever comes first), and ELT batteries that are due to be replaced upon expiration. These special date items, regardless of the date of approval for return to service, are due based upon a specific date associated with the part itself. That date must be captured and recorded in the maintenance logbook entry as well.
Leap frogging
Another factor that enters the discussion is what I refer to as “leap-frogging inspections.”
Several years ago, the FAA began to focus on the completion date of inspections and the calculation of the next due time and identified a problem in some inspection programs that inadvertently allowed for extra time between inspections. The problem came when the inspection program allowed a tolerance window that included both a plus and a minus tolerance around a next due time. For example, a scheduled maintenance item that is due every 500 hours with a plus or minus 50-hour tolerance, as called out by the inspection program recommended by the manufacturer, could be accomplished between 450 hours and 550 hours in accordance with that program. When the inspection is accomplished prior to the due time, say at 475 hours, the next due is technically still at 1,000 hours. The leap frogging occurs if and when the operator uses the whole 50-hour-plus window again and doesn’t accomplish the inspection again until 1,050 hours. In that case, the intended 550-hour maximum interval (500 hours plus 50 hours) has been exceeded by 25 hours, or leap frogged. (I know, it’s a silly term.) The FAA does not want us ever to exceed the interval specified by the manufacturer plus any allowable over fly tolerance in any case. Every manufacturer handles this differently but usually addresses it within the language of the inspection program preamble itself.
The leap frogging idea also applies to calendar items and that is where the confusion comes in. In some cases, it can appear that the aircraft was flown past the calendar due date if, while down for maintenance, the due date plus any allowed over-flight tolerance comes and goes. In that case, the resulting approval for return to service date would be a date past the original due date.
Unlike hours and cycles/landings, calendar time continues to accumulate even when an aircraft is down for maintenance. The difference here is that for the purposes of scheduled maintenance, calendar scheduled maintenance items (with the exception of special date items) calculate their next due from the date of approval for return to service. The determination of whether or not an inspection item is overflown (the interval plus any allowable overfly) is based upon when the aircraft is brought out of service and placed into a maintenance event, not the approval for return to service date that follows the maintenance. Better said, you are not in violation if you don’t operate the aircraft past the due date, and that doesn’t change or determine the next approval for return-to-service date.
In summary,
1. Approval for return to service is a function of maintenance personnel.
2. Returning an aircraft to service following maintenance is accomplished by a pilot.
3. No maintenance is complete until the maintenance record entries required by FAR Part 43.9 and 43.11 are completed.
4. The entire work scope is signed off and approved for return to service on the same date only after completion of the maintenance event.
5. Passing a due date while in maintenance is not a violation. The aircraft must be operated or flown after a calendar requirement has expired.
I hope this article has been helpful. In the interest of the aircraft operator and maximizing aircraft availability, let’s be sure that when we are calculating the next due scheduled maintenance, we calculate that date properly by basing it upon the appropriate date of approval for return to service.
Joe Hertzler has more than 25 years of experience in business aviation. He has earned a reputation as an efficiency expert when it comes to aircraft maintenance and is well known for his in-depth understanding of maintenance regulations and how they affect aircraft compliance. He has helped many in dealing with critical and urgent FAA interactions and often speaks on the topic of aircraft maintenance and compliance at industry events, such as the NBAA Maintenance Managers Conference, PAMA meetings and IA renewal seminars. Hertzler also serves on the National Air Transportation Association’s (NATA) Maintenance and Systems Technology committee. JoeHertzler@gmail.com.